One of the key exhibitions this year is Growing Home at the National Museum of Scotland, exploring the past and future of materials and how biomaterials – like fungi – can be used for fashion, engineering and more.
Part of this special exhibition is Symbio from Edinburgh-based artist Emily Raemaekers, featured in the picture. Her garment uses mycelium materials and leather made from vegetable processing waste in combination with cutting edge environmentally-friendly fabrics. Adorned with elaborate laser cut designs inspired by mycelium structures, hand carved lino print patterns and featuring plant-derived biomaterial dyes. Her work highlights some of the key issues in the fashion industry nowadays such as textile dyeing being the second largest polluter of water globally.
Emily Raemaekers is an Edinburgh-based designer who specialises in garment design and construction, and hand printed fabrics. She studied Performance Costume Design at Edinburgh College of Art before working as a freelance Costume Designer in the Scottish theatre and film industry. Emily ran a textile printing and fashion accessory business for 10 years in Scotland and Australia, and dabbled in upholstery, before moving back to her hometown of Edinburgh where she is now a events planner, blending creativity and the arts with science.
Symbio is a collection of biomaterial themed garments inspired by fungus structures. Many of the most exciting and talked-about biomaterials being developed today are made from mushrooms, and the designer has used this as the inspiration for these garments. The designer has explored the properties of a range of biomaterials using a variety of construction methods. Bracket fungus-like elements are attached using appliqué, an ornamental needlework technique. The elaborate cape structure is created using laser cutting.
The base dress is dyed with dried hibiscus flowers, a biomaterial dye that produces a rich palette of pinks and reds. Industrial textile dyes contain many harmful chemicals derived from fossil fuels, and textile dyeing is the second largest polluter of water globally. Many designers are now exploring natural dyes derived from plants, invertebrates, and minerals traditionally used by many cultures around the world. Although it is more difficult to produce consistent tones from natural dyes, this variation can be embraced as an aesthetic choice as part of the Slow Fashion movement.
The dress is decorated with mycelium patterns using linocut, a printmaking technique where linoleum is carved into to create a relief surface. The designer has printed these using water-based textile inks which are more sustainable than commonly used plastic-based alternatives.
The dress itself is made from Tencel(TM), a type of lyocell — a fibre made from wood pulp. As the raw material is responsibly forested wood, the textile originates from a renewable source, and Tencel(TM) uses a closed loop manufacturing process. The fibres are also certified as compostable and biodegradable, making Tencel(TM) one of the more sustainable options for the fashion industry which are currently available on an industrial scale.
The designer has chosen a range of cutting-edge biomaterials to create the mushroom-like appliquéd elements that adorn the garments. Some are made from Uppeal(TM), a leather made from apple processing waste leftover from the juice and compote industry. The apple fibres are made into a powder and mixed with polyurethane, then laminated onto cotton and polyester. Apple waste makes up 20% of the final textile and every meter contains 5 apples. By using waste, Uppeal(TM) helps to create a circular economy which supports the planting of fruit trees and provides a second income for farmers. It also reduces the amount of plastic-based fibres required to make a leather textile and is an interesting alternative to traditional leathers made from animal skin, as animal farming uses 83% of global farmland and is responsible for 60% of agriculture’s greenhouse gas emissions.
MuSkin is also used for some appliquéd elements. This is an alternative to animal leather made from a large parasitic fungus that grows wild in subtropical forests. Every piece of MuSkin is unique, 100% natural and does not use any chemicals or plastics in the production process. This fascinating material is designed to offer an innovative, low-carbon alternative to materials that use fossil fuels in their manufacturing process. Animal leather has a significant carbon footprint, as livestock farming uses a lot of fossil fuels to power farm machinery the produce animal feed, and clearing land for livestock is responsible for much of the world’s deforestation. Animals also produce a lot of methane, a big contributor to greenhouse gases.
Other appliquéd elements in these garments include SeaCell(TM), a new lyocell fabric that uses 19% algae in its fibres. Whilst a good example of a biodegradable fibre, the brand has faced some controversy for its claims that minerals and vitamins can be absorbed through skin contact with the fabric. As industrial interest in biomaterials increases, global scrutiny of any associated claims of green or health credentials also rises.
Some more traditional biomaterials are featured in the garments, including:
- Silk, a protein fibre made from the cocoons of certain insect larvae.
- Cork, a biodegradable fibre made from tree bark. Cork is sustainable as the tree is not cut down in the harvesting process; the stripped bark regenerates and the tree continues to grow.
- Linen, a natural textile made from the fibres of the flax plant. Linen is a sustainable choice for the garment industry because the entire flax plant can be woven into a fibre, making it a zero-waste crop. It also takes dye extremely well, and the linen used in this art piece has also been dyed using hibiscus flowers.
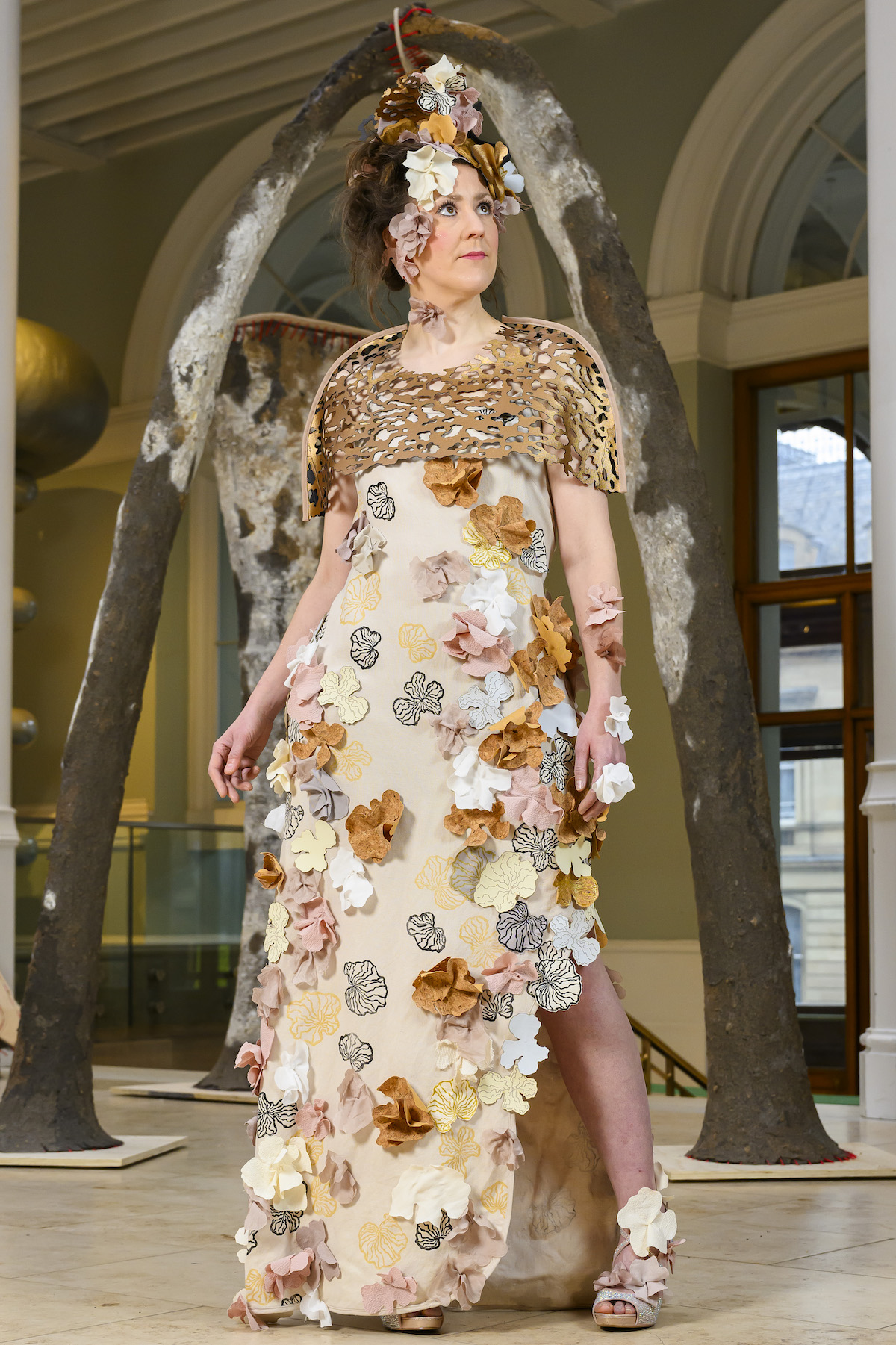